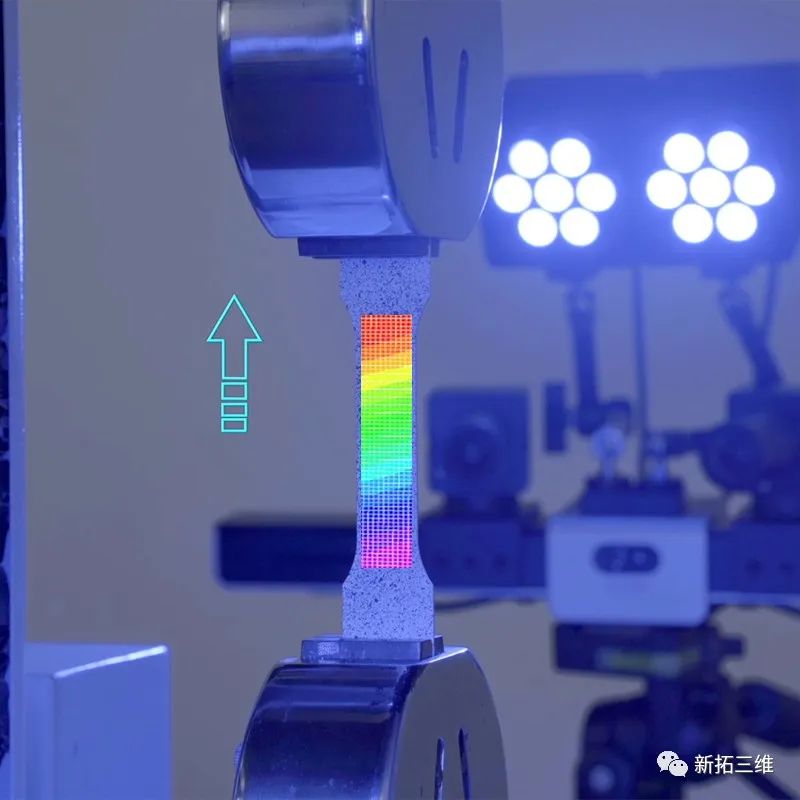
【知识分享】图像相关法(Digital Image Correlation 简称DIC)三维全场应变测量VS应变片实际测试精度比较分析
新拓三维XTDIC三维全场应变测量系统,可以测量材料表面及结构的力学表征,通过DIC软件计算输出材料表面的位移场、应变场等数据,可分析材料在加载过程中裂纹萌生、演化、扩展和弹塑性阶段的动态变化,稳定可靠的测试数据有助于科研人员更高效、精确地完成研发测试。然而,应变片也有不足的地方,单应变片仅能测量单个方向的应变;数字图像相关法(DIC)基本原理是摄像机采集物体在同一时刻的散斑图像,经过匹配、重建得
在人类文明发展的历史过程中,由于材料性能的不合格造成的大大小小的事故不胜枚举。像1912年泰坦尼克号的沉没,1938年二战前夕英国皇家空军Spitfire战斗机的坠落,1998年德国的铁路惨案……
当一个新的材料从单个产生到行业应用,其中力学性能检测是必不可少的一环。材料受力后会产生变形,变形到一定程度即发生断裂,这种在外载作用下材料发生材料变形与断裂的行为,即为材料的力学性能。
电阻应变片的诞生,让材料的力学性能定量描述成为了现实。金属电阻材料受到外部拉伸力或压缩力时,就被拉伸或缩短,其电阻值亦随之增加或降低。
然而,应变片也有不足的地方,单应变片仅能测量单个方向的应变;大幅面工程测量需采用应变花,但引线非常会增加额外质量;另外,对于特殊材料表面,或者在特殊环境(温度、湿度等)下,应变片有诸多使用限制。
-01-
DIC与传统测量技术
数字图像相关法(DIC)基本原理是摄像机采集物体在同一时刻的散斑图像,经过匹配、重建得到物体表面点的三维坐标,比较这些点在变形前、后的三维坐标变化,得到物体表面点的位移和变形。
与传统传感器(如应变仪)的点测量不同,DIC技术能够对三维变形形状进行全场分析,可以在一个区域内提供来自更多数据点的测量数据,而不会干扰物体本身的自重和载荷情况。
对于测量设备来说,测量精度是至关重要的。DIC技术的精度主要由硬件参数、理论算法、以及测试距离以及视场宽度决定。那么,DIC全场应变测量设备在实际测试中的精度是多少?与接触式应变片测量相比,它的表现又怎么样呢?下面通过一个加压变形测试案例,为大家展示DIC技术的测量精度与数据可靠性。
新拓三维XTDIC三维全场应变测量系统,可以测量材料表面及结构的力学表征,通过DIC软件计算输出材料表面的位移场、应变场等数据,可分析材料在加载过程中裂纹萌生、演化、扩展和弹塑性阶段的动态变化,稳定可靠的测试数据有助于科研人员更高效、精确地完成研发测试。
-02-
零部件受压加载变形测试
为了验证DIC技术的测量精度,对结构部件在实际工况下进行抗压强度测试,分析受压加载关键区域的变形情况,通过与应变片比较测量精度情况。
在结构部件表面粘贴应变片,采用XTDIC三维全场应变测量系统进行图像采集,将应变片测试数据与DIC测量结果进行比较,通过实际测试数据验证DIC仪器设备的测量精度。
-03-
DIC测量数据与应变片数采对比
测试过程,首先输出DIC测量应变场,绘制出关键点应变;然后,用DIC测量数据与实际应变片数据进行对比,可以看到XTDIC三维全场应变测量系统输出的数据与应变片值吻合很好,两者应变差别在20με以内。
-04-
DIC测量数据-应变场解算
DIC测量数据-应变场解算
如图所示,在DIC软件中将该点数据导出,可在EXCEL表格绘制出该点应变:
从上图可以看出,结构部件加压一共分为两个阶段,在三个不同位置DIC测量输出的平均应变数据分别为:
在三个不同加压状态下,DIC测量出来的应变数据分别为:0.000285%(0.285微应变)、0.00931%(93.1微应变)、0.0205896(205.896微应变)。
在三个不同加压状态下,对应应变片测出来的数据为:0.206微应变,73.552微应变,217.215微应变(如下面应变片数采图所示)。根据对比,两者应变相差分别为0.085微应变,19.5微应变,11.3微应变,则应变精度相差均在20微应变之内。
静止状态应变片数采图
第一次加压应变片数采图
第二次加压应变片数采图
综上所述,经过三组加压实验测试,新拓三维XTDIC三维全场应变测量系统测试精度与应变片数采精度验证对比,应变数据大小差距在20个微应变之内。
DIC方法被广泛应用于常规静态测量、高速冲击测量、疲劳全场测量、瞬态振动与模态测量、3D温度场与应变场耦合、微小尺寸材料力学性能测量之中,在科研领域与工程应用领域已经受到了众多科研工作者、工程师的认可。
更多推荐
所有评论(0)